When producing insulated glass, the first and most critical step is glass cleaning. As a preliminary phase in the manufacturing process, achieving proper cleaning standards is essential, yet this step is often underestimated or misunderstood. So how can you choose the right glass washing machine? Let’s break it down by category. The two primary types on the market are absorbent roller hot air drying machines and cold air drying machines. If your goal is optimal cleaning, a cold air machine is the ideal choice.
Types of Glass Washing Machines and Their Features
1. Absorbent Roller Hot Air Cleaning Machine
This machine relies on absorbent rollers to remove water, followed by hot air drying to achieve a clean surface. However, this process can leave an invisible thin film on the glass surface due to water mist formed during drying. This thin film reduces adhesion between the glass and sealant, potentially shortening the lifespan of insulated glass.
Advantages:
- Affordable price
- Simple structure
- Low noise
- Small footprint, suitable for small-scale window and door factories
Disadvantages:
- Slower speed compared to cold air machines
- Lower glass cleanliness
- Unsuitable for coated and LOW-E glass cleaning
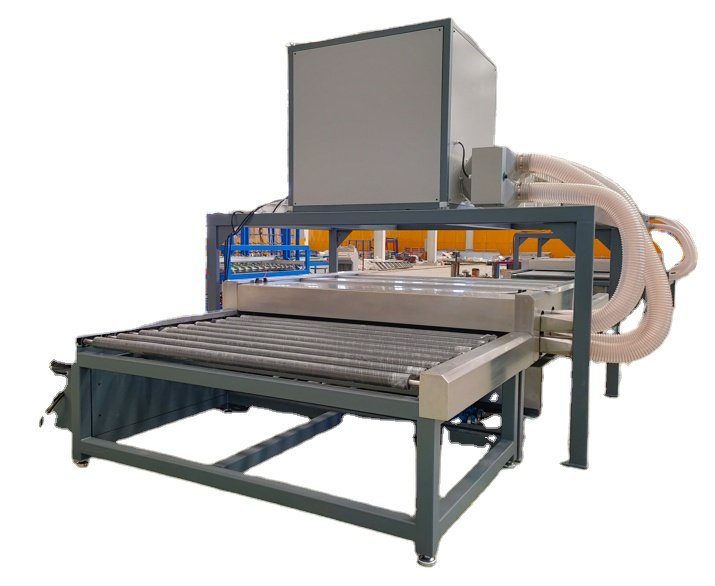
2. Cold Air Drying Cleaning Machine
Our independently developed cold air drying machine has been in the market for ten years, receiving positive feedback for solving issues like low cleanliness and production inefficiency in insulated glass manufacturing. This machine uses stainless steel components for water contact areas, a high-pressure water pump, a heated water tank, and three pairs of brushes. It can clean coated and LOW-E glass as needed and uses strong cold air for drying. While slightly noisier, it offers excellent cleaning results and faster speeds, making it a must-have for professional insulated glass production.
Advantages:
- Corrosion-resistant
- High speed and efficiency
- Superior cleaning results
- Long service life, ideal for medium to large-scale enterprises
Disadvantages:
- Slightly higher noise levels
- Requires moderately clean water for operation
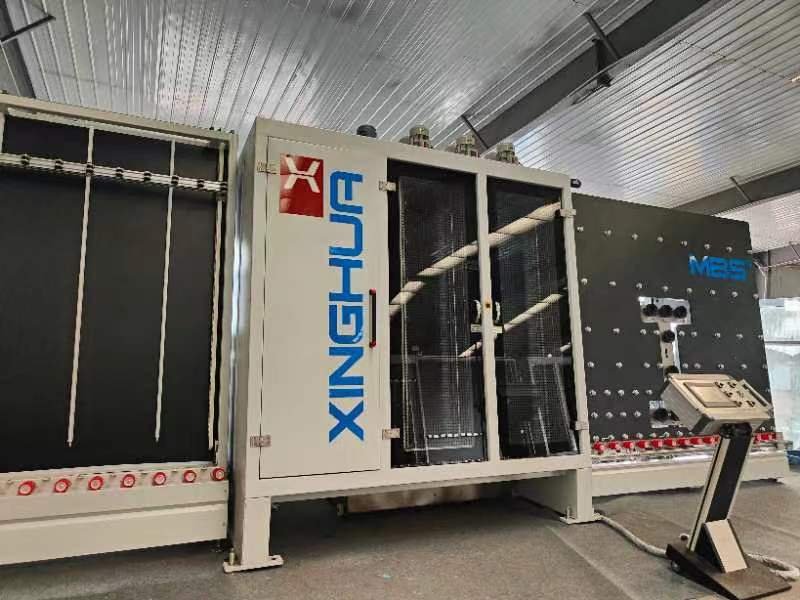
Comparison Table of Glass Washing Machines
Feature | Absorbent Roller Hot Air Machine | Cold Air Cleaning Machine |
Glass Types | Flat glass, small tempered glass | Flat, tempered, coated, LOW-E glass |
Cleaning Speed | 0–2.5 meters/min | 0–6 meters/min |
Frame Pipe Thickness | 1.4 mm | 2.2 mm |
Transmission | Chain and sprocket | Helical gear |
Brush Material | Plastic bristles | High-elastic wear-resistant 1010 nylon |
Protective Cover | Thin iron plate with electrostatic spray | Stainless steel brushed plate |
Water Splash Guard | Rubber | Stainless steel brushed plate |
Water Tank Material | Stainless iron plate | Stainless steel plate |
Water Tank Quantity | 2 | 3 |
Brush Quantity | 2 Pairs | 3 Pairs |
Pre-cleaning Spraying | None | Yes |
Glass Feeding Mechanism | Universal wheels | Rubber roller transmission |
Water Tank Heating | None | Yes |
Noise Level | Low | Moderate |
Cleaning Results | Second pollution, static issues | Clean, transparent, static-free |
Lifespan | 3-5 Years | 8+ Years |
Price | Lower | Moderate |
Why Choose Cold Air Cleaning Machines for Insulated Glass Production?
- High Cleanliness: Cold air machines ensure a transparent, static-free surface, critical for glass bonding and durability.
- Efficiency: With a cleaning speed of up to 6 meters per minute, production timelines improve significantly.
- Versatility: Capable of handling various glass types, including coated and LOW-E glass, meeting diverse production needs.
- Durability: Constructed from high-quality stainless steel and wear-resistant components, these machines offer a lifespan exceeding eight years.
For businesses aiming to excel in insulated glass production, investing in a cold air glass washing machine is a strategic choice. It guarantees superior cleaning results, enhances efficiency, and reduces long-term operational costs, making it the preferred equipment for medium to large enterprises.
Optimize your glass cleaning process today with the right equipment and elevate your production standards!