Introduction to Insulating Glass (IGU)
Insulating glass units (IGUs) are crucial for improving energy efficiency and comfort in modern buildings. They provide excellent thermal insulation, noise reduction, and prevent condensation. Understanding how insulating glass is made will shed light on its benefits and applications.
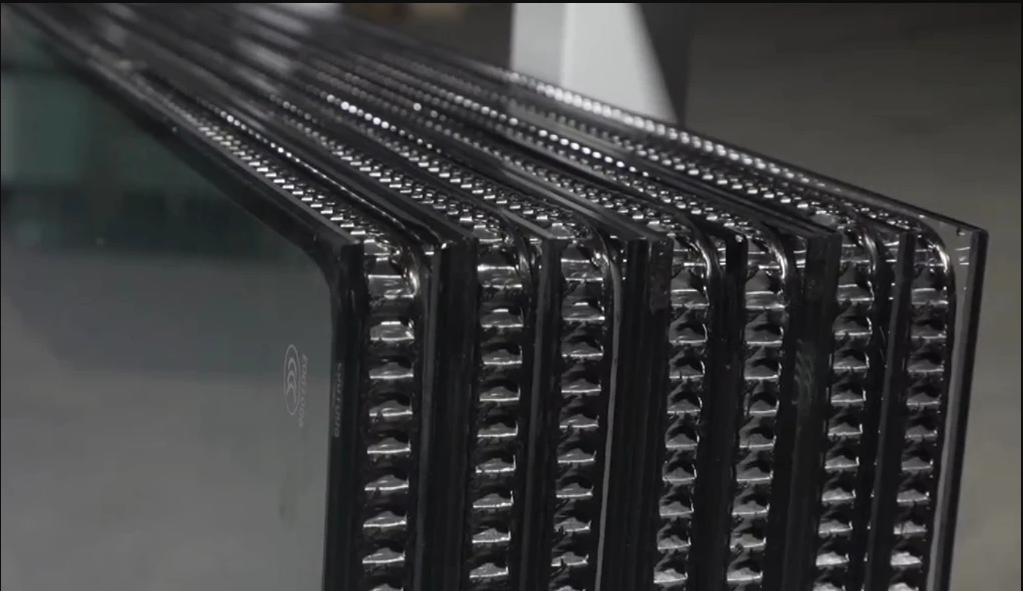
What is Insulating Glass?
Insulating glass is made up of two or more glass panes separated by a spacer and sealed to create an airtight unit. This design traps air or gas between the panes, acting as an insulator that reduces heat transfer.
Step-by-Step Process of Making Insulating Glass
- Glass Washing and Drying
Washing: The glass panes are cleaned in a washing machine to remove any dirt, oil, or other contaminants that could affect the adhesion of sealants or spacers.
- Spacer Application
Spacer Material: A spacer, usually made of aluminum, stainless steel, or flexible warm-edge materials, is cut to size and shaped according to the glass dimensions. Warm-edge spacers reduce thermal bridging and improve energy efficiency.
Desiccant Filling: The spacer is filled with a desiccant (moisture-absorbing material) to prevent condensation inside the unit.
Spacer Installation: The spacer is applied to the perimeter of one of the glass panes using automated or manual equipment. The spacer must form a continuous and sealed barrier around the edge of the glass to maintain gas tightness.
- Primary Sealing
Butyl Application: A layer of butyl sealant is applied to the spacer’s edge where it contacts the glass. This provides an airtight and watertight seal, ensuring the unit’s longevity.
- Glass Assembly
Pairing Glass Panes: The second pane of glass is aligned with the spacer to create the insulated glass unit. If it’s a triple-glazed unit, a third pane and spacer are added.
- Gas Filling (Optional)
Filling with Nobel Gas: To improve the thermal performance of the IGU, the space between the panes can be filled with an inert gas like argon, krypton, or xenon. These gases have lower thermal conductivity than air, reducing heat transfer.
- Secondary Sealing
Sealant Application: A secondary sealant, usually polyurethane, polysulfide, or silicone, is applied around the edges of the glass unit. This sealant reinforces the structural integrity and ensures long-term protection from moisture ingress.
- Quality Control
Inspection: The completed IGU is inspected for visual defects, including seal integrity, gas fill level, and overall quality.
Testing: Advanced lines may include automated testing for argon fill levels, unit dimensions, and gas leakage to ensure compliance with industry standards.
- Storage and Packaging
Curing: Some sealants may require a curing period before the IGU can be packaged.
Packaging: The units are then stacked on racks and prepared for shipment or further processing.
Automation in IG Production
In modern insulating glass production lines, many of these steps can be fully automated, such as glass washing, spacer application, gas filling, and sealing. This reduces labor costs, increases production speed, and improves quality consistency.If you want to explore flexible warm-edge spacers IGU production process please click here.