In today’s world, where building safety and energy efficiency are key concerns, insulating fireproof glass plays a critical role. It not only prevents heat loss but also provides an essential barrier in case of fire, making it a preferred choice for modern architecture. Whether you’re in the glass manufacturing industry or curious about how this specialized glass is made, this article will guide you through the process.
- Afastgrowing market
The global fireproof glass market is projected to grow at a Compound Annual Growth Rate (CAGR) of around 8-10% between 2024 and 2030, reaching a market size of $7-10 billion by the end of this period. This growth is being driven by stringent fire safety codes and regulations across various regions, particularly in developed and emerging economies.
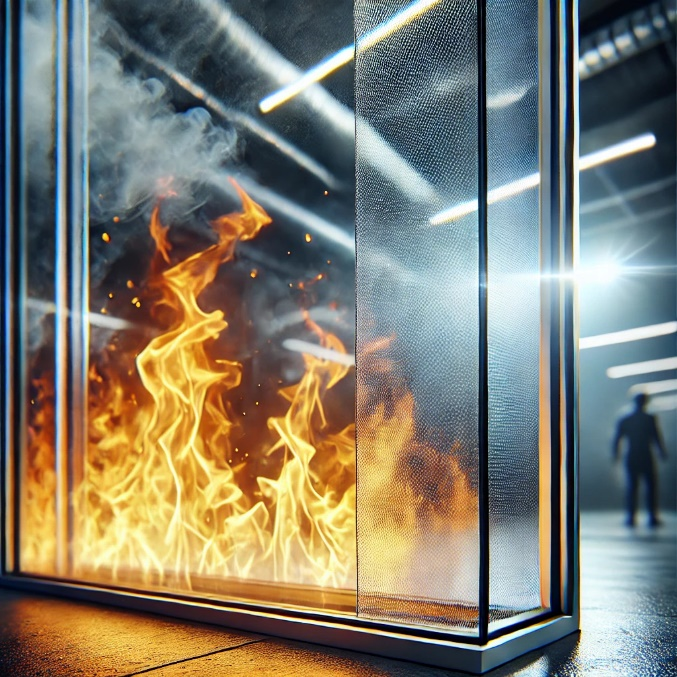
- What Is Insulating Fireproof Glass?
Insulating fireproof glass is a type of glass that offers both thermal insulation and fire resistance. It is commonly used in building facades, doors, windows, and partitions to protect against both heat loss and fire hazards. The glass is made by combining layers of glass with fire-resistant interlayers or special coatings that can withstand extreme temperatures for extended periods.
- Benefits of Insulating Fireproof Glass
Before diving into the production process, let’s briefly look at the benefits:
*Fire Resistance*: Can withstand high temperatures and prevent the spread of fire.
*Thermal Insulation*: Reduces energy costs by maintaining indoor temperatures.
*Sound Insulation*: Provides noise reduction, making it suitable for urban environments.
*Safety*: Prevents shattering during a fire, offering a safe barrier.
*UV Protection*: Some versions protect against harmful UV radiation.
- HowMBS FireproofGlass Production Line Making Insulating Fireproof Glass
Our production procedures can be divided into two sections, first section is fully automatic process including auto glass loading, glass washing, auto spacer application, auto glass assembling and roll pressing. The second section is semiautomatic processes including edge sealing, fire retardant liquid mixing and pouring, thermo-curing.
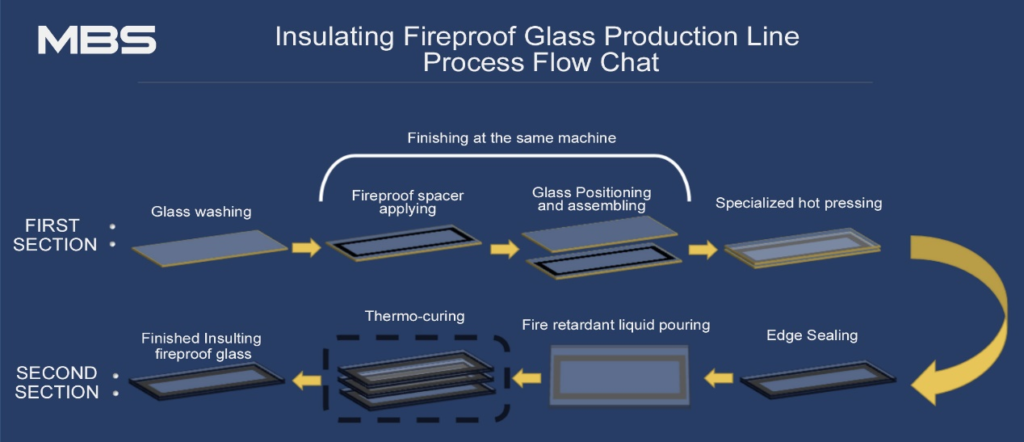
4.1. Input glass size, fireproof sealing spacer size, number of glass layers, and pressed glass thickness into the control panel. After the glass washing machine, cleaned glass is accelerated and transmitted to the spacer applicator by the first conveyor.
4.2. The spacer applicator automatically replaces the suction cup according to the size of the glass, holding the glass and completing the sealing spacer applying process automatically.
4.3. After the fireproof sealing spacer applied on the glass pane, it is directly placed in the automatic assembling station, and its automatically completed according to the set number of glass layers.
4.4. After the fireproof glass assembling is completed, it is transmitted to the intelligent heating section through a convey table, the infrared heating device radiates evenly heat to the glass edges and each layer of sealing spacer according to its size.
4.5. After heating, the glass transferred to the progressive roller pressing section, the rollers need to gradually pressed with high pressing accuracy.
4.6. The laminated glass is transferred by the third conveyor, which can be directly unloading or connected to a sealant extruder.
4.7. Pouring the fire-retardant liquid.
4.8. Put the glass into the curing furnace.
Overall, automating the production of insulating fireproof glass enhances both quality and efficiency while reducing costs and risks. Looking to fully automatic production line for insulating fireproof glass? Contact our experts today to learn more about the best solutions for your project.