In the competitive insulated glass (IG) manufacturing industry, efficiency, precision, and energy conservation are crucial for growth and profitability. If you’re an aluminum IGU manufacturer looking to upgrade your current production line, one simple solution can make all the difference: MBS’s Warm Edge Upgrade Set. By integrating this upgrade set with your existing IG line, you can achieve fully automatic production with flexible warm edge spacer technology, significantly improving productivity and product quality.
Why Upgrade to a Fully Automatic Flexible Warm Edge Spacer IG Line?
Adding MBS’s Warm Edge Upgrade Set to your aluminum IG line not only brings advanced technology but also helps you streamline processes, save on labor costs, and reduce energy consumption. Let’s look at how each component of this upgrade can transform your IGU manufacturing.
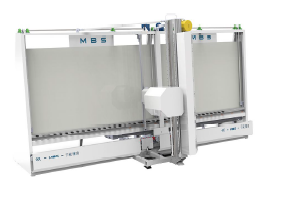
Key Components of the Warm Edge Upgrade Set
- Automatic Spacer Applicator
The automatic spacer applicator is designed to quickly and accurately apply flexible warm edge spacers with precision. Using multi-axis servo linkage technology, the applicator ensures that the spacer is positioned consistently on each pane. This boosts production efficiency and reduces labor requirements while delivering spacers that are perfectly aligned and well-distributed for every unit of double or triple glazing glass.
- Spacer Heating Technology
Our intelligent heating system is engineered to focus heat only on the spacer, avoiding unnecessary heating of the glass chamber. This targeted heating approach ensures that the spacers are applied with the ideal adhesion properties while reducing energy consumption. The heating lamp is programmed to activate only when the glass pane is in place, optimizing energy usage and preventing unnecessary heating of the workspace.
- Corner Seal Machine
For optimal sealing and finishing, the corner seal machine automatically seals the final corner after gas filling. This step completes the insulation process with a precise, automated touch that enhances the durability and energy efficiency of the IGU, ensuring a tight seal that’s critical for long-lasting quality.

Benefits of the Warm Edge Upgrade Set for Aluminum IGU Manufacturers
- Enhanced Efficiency: With automation handling spacer application, spacer heating, and corner sealing, your line will experience faster production cycles, enabling you to meet higher demand.
- Improved Product Quality: Consistent application of spacers, with precise heating and secure sealing, means each IGU produced meets high standards of quality and durability.
- Labor Cost Savings: Automated processes reduce dependency on manual labor, helping to cut costs and ensure consistent output with less human intervention.
- Energy Savings: Intelligent heating and energy-conserving features mean reduced operational costs and a more eco-friendly production line.
Upgrade Your IGU Production Line Today
If you’re ready to transform your aluminum IG line into a fully automated system with flexible warm edge spacer technology, MBS’s Warm Edge Upgrade Set is the solution you need. Contact us today for more information on how we can help you achieve a higher level of productivity and product quality in your IGU manufacturing process.
Take the first step toward a more efficient, high-quality, and cost-effective production line. Reach out to MBS and let us assist you in upgrading to a fully automatic flexible warm edge spacer IG line.